如何优化注塑成型的每个元件
John Ji | 15 9 月, 2021
设计和制造注塑模具需要花费数天和数周的时间,这是设计人员面临的最糟糕的状况。 当生产最终开始时,第一个元件从模具中脱离时,一个令人头疼的意外情况发生了—模制件的表面具有凹痕,这些凹痕不仅看起来难看,而且可能会影响零件的性能。
为什么会这样?
这种现象被称为收缩。注塑过程中,工程塑料材料会受热膨胀,而在冷却时,成型的塑料部件会在模具中收缩–收缩系数在零件体积的0.2%至2%之间。这是物理学层面上决定的,也是不可避免的。问题是注塑部件本身无法均匀收缩。 尽管零件的外表面迅速冷却,但在零件的内部以及部分尺寸厚度较大的区域内,该过程花费的时间更长。同时这会在塑料零件内部造成应力。 它们会导致部分外表面塌陷并出现裂纹。此外,内部还有可能形成空腔的风险–微孔至气泡状的空腔会降低零件的强度和尺寸稳定性,外表面的变形和内部的空腔的都会导致零件的尺寸公差难以控制。
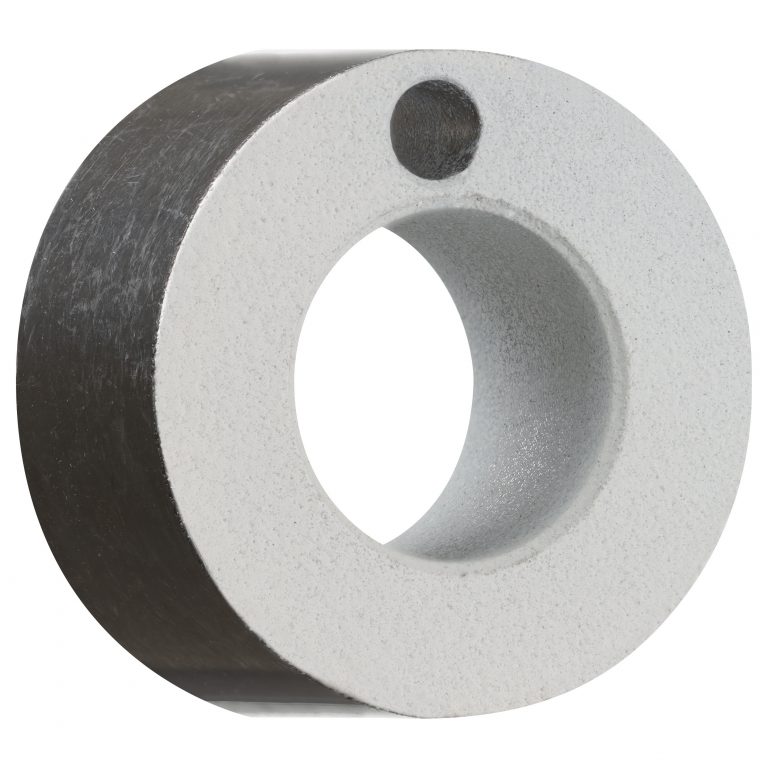
解决方案:避免注塑成型中的壁厚
在设计阶段要牢记收缩现象,以避免上述不良结果。这可以通过避免设计较厚的壁厚来避免材料的聚集。根据材料的不同,理想的厚度在0.5至2毫米之间。例如,如果零件存在类似拐角的结构,这会导致材料积聚,建议可以采用拐角位置内侧设计独立的柱形结构,并搭配壁厚较薄的加强筋进行连接,这可以有效解决局部材料聚集导致的应力集中,保持部件良好的尺寸控制,同时加强筋的设计可以有效保证该位置的结构强度。
但是,如果无法减小壁厚怎么办?
在我们的免费的《注塑成型设计指南》中可以找到有关如何进一步减小注射成型零件的壁厚以及如何通过其他不同措施在模具注塑生产中节省大量成本的信息。