Additive manufacturing in special vehicle construction
Lynna Liu (刘银) | May 6, 2020
Motorists with disabilities benefit from “Darios”, a digital gas ring. This allows you to give throttle with your hands on the steering wheel. “Darios 211” consists of over 200 identical parts that slide over the flattened steel ring. These parts consist of iglidur® I3 and are manufactured in 3D printing.
KEMPF was founded in 1955 by Hans Kempf who had lost the use of his legs after contracting polio.He invented the accelerator ring to be able to drive with both hands on the wheel.By the end of his life in 2002 he had adapted over 100 000 vehicles.
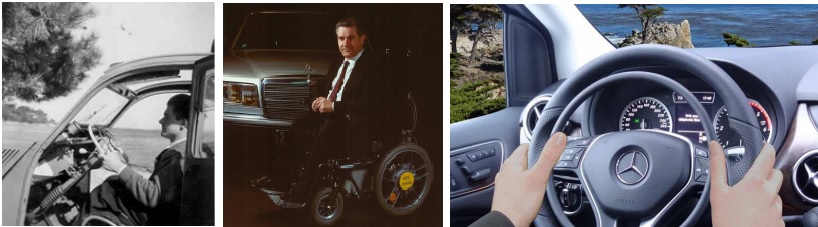
Pic.1 Mr.Hans Kempf and his invention
How does the gas ring work?
The company KEMPF develops equipment in the field of special vehicle construction,to be more precise, for disabled drivers. Darios, the digital gas ring, allows a driver who cannot use his legs to accelerate with his hands on the steering wheel. The sleeve of the steel ring must rotate freely so that the driver can easily control the acceleration when leaving a curve; the steering wheel then slides back into straight position with his fingers.
What was the customer’s problem?
Common design – round steering wheel.Thers is no problem that being used since many years. New designs– edged steering wheel,in which the ring needs to move around the edge! As long as the steering wheels were round, the case was a plastic part covered with leather. Now more and more steering wheels are flattened, so a solution had to be found to keep the sleeve turning freely over a flattened ring. A special component with the geometry of the glider by mechanical processing to manufacture was impossible.
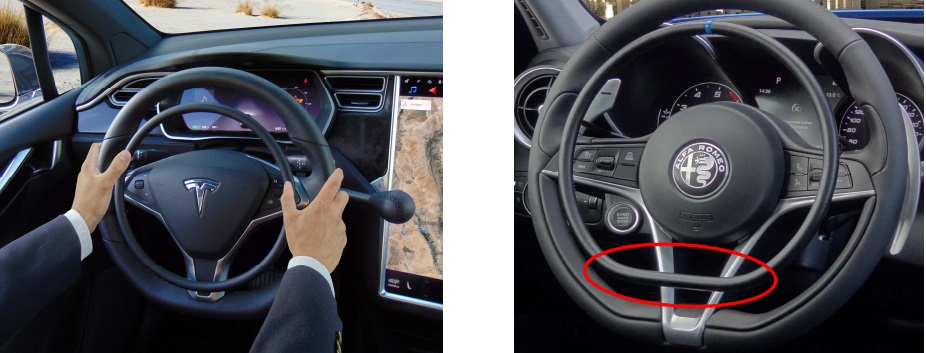
Pic.2 New challenge at the Accelerator ring :common round and new flattened steering wheel
The solution
DARIOS 211 ,one of the latest model, consists of over 211 identical small parts that slide over a flattened steel ring. These parts are manufactured in iglidur® I3 by the igus® 3D printing service. The most important advantage of iglidur® I3 is that no lubrication is necessary. This is very important as the company KEMPF offers a 30 year warranty for all its equipment. The parts are covered with elastic leather. The ring looks elegant and the customers are enthusiastic. The 211 special sliders which are mounted to one ring,should be special designed. The concept has undercuts in all directions that injection molding should be very expensive,while no problems with additive manufacturing. make the ring elastic enough to be able to slide around the edge.
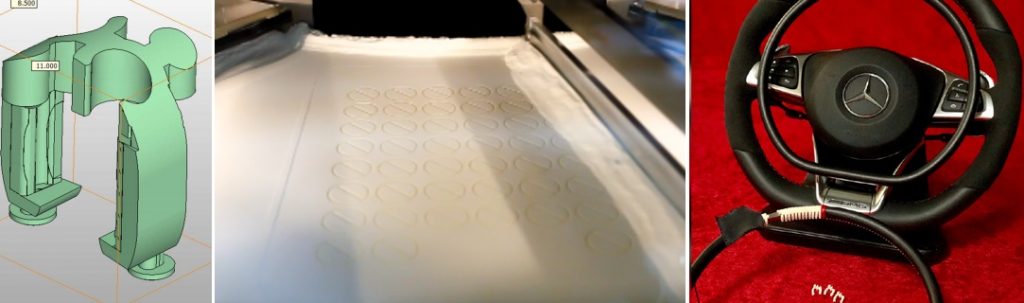
Pic.3 Technical drawing of one of the individual components made of iglidur® material, which glide on the steel ring.
Why additive manufacting at igus?
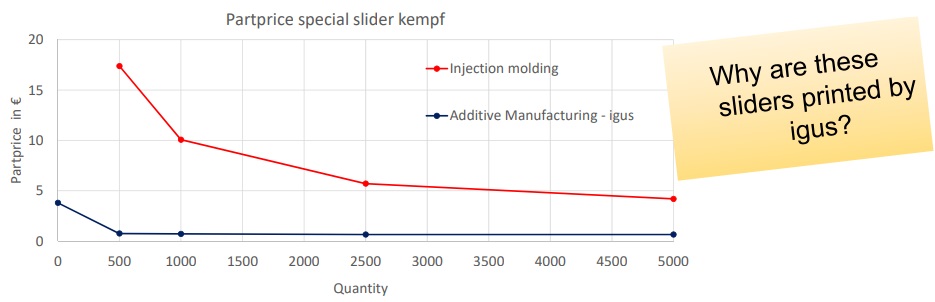
Pic.4 cost comparison between injection molding and additive manufacturing
The cost comparison self-explained addictive manufacturing cost-efficiency. Injection-moulding need 7300 € tooling costs and supplier only quotes for segmented production.For additive manufacturing (igus-SLS):3.8 € at quantity 1,and partprice below 1 € from 500 pieces on.
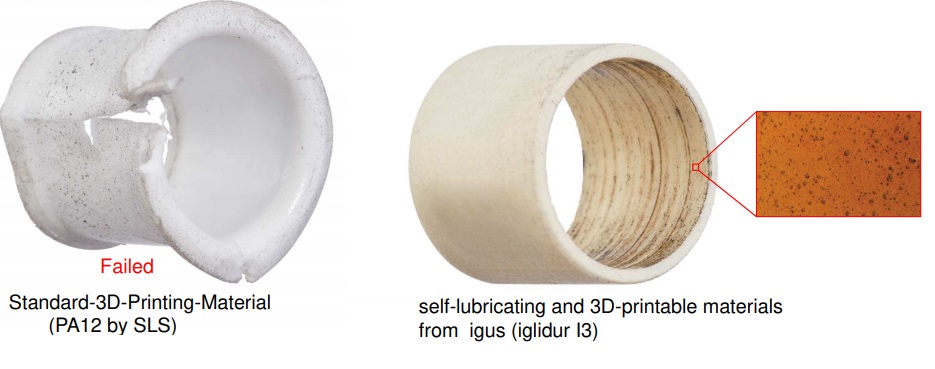
Pic.5 3D-printed bearings in test-rig: rotating 20 MPa ( 800 kg on a 20 mm bearing)
3D-printing-materials from igus are self-lubricating.3D printed bearing have similar wear-resistance compared to regular bearings.Compared to regular plastic material,like PA12, our iglidur i3 shows perfect wear-resistance.
video. “Darios 211” gives throttle with your hands at the steering wheel