Lubrication-free synchronisation with plain bearing technology
Ahren Xia | February 4, 2021
There are many different possibilities to synchronise several adjustments in one system. But which is the right one for me and my application? Often not easy to answer. But what if it should be simple and uncomplicated?
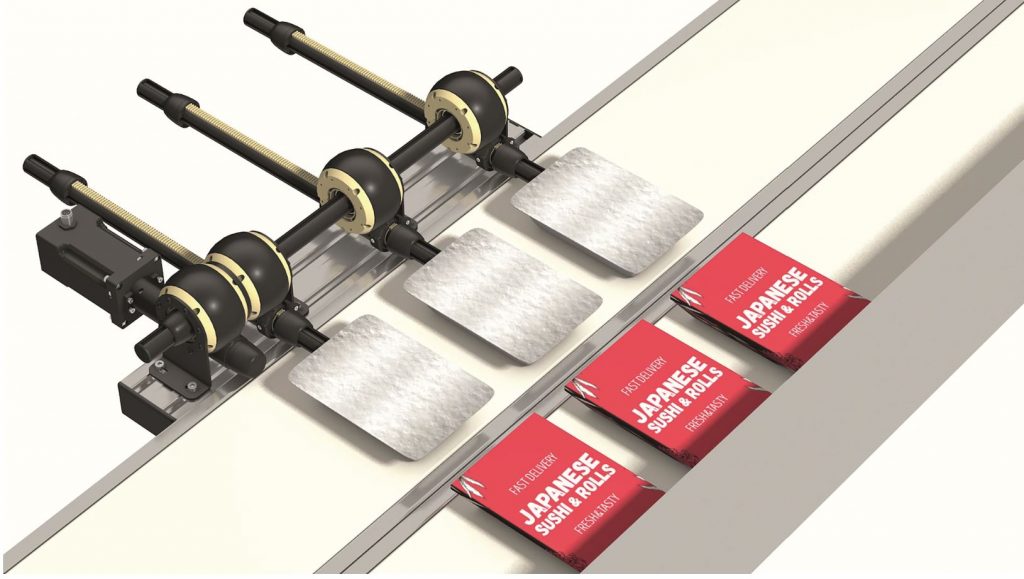
What are the options?
The market offers different solutions for different applications. The most commonly used system is a metal angular gear. Here you will find the largest offer. A variety of sizes and designs are available. There is also a suitable solution for large power transmissions. Usually these gearboxes are expensive and require some maintenance.
Another possibility is the open design of an angular drive with bevel gears. The solution is simple in design and cost-effective. Due to its open design, however, it is susceptible to contamination and requires regular lubrication. Not to be ignored is the risk of injury to personnel due to the exposed gears.
What is the alternative?
Angular drives made of high-performance polymers. We have dealt with the problems of standard market solutions and have adapted our robolink D angular drives from the robolink modular system for this purpose. The new Apiro components are also ideally suited for synchronisation tasks. The angular drives provide everything that is necessary. But above all, the gearboxes have a huge advantage: they are maintenance-free and lubrication-free. The installed components are made of polymer, which guarantees dry operation. This has several very clear advantages.
https://www.igus.com.cn/info/modular-robot-gears-apiro
If we move with the gearbox in an area that is heavily dirty, the dirt particles cannot adhere to the grease in the gearbox. Similarly, there is no risk of the lubricants being flushed out of the gearbox when the system is cleaned. No maintenance or relubrication is required and product contamination is excluded. The good corrosion resistance due to the components used also plays an important role, especially if the application is in the beverage or food industry. Here, cleaning is often done wet and with chemicals, which can cause problems for metallic solutions.
https://www.igus.eu/info/industries-beverage?L=en
The majority of the components used are manufactured by polymer injection moulding and offer a great cost advantage over metal solutions. Another important aspect is the service life. Through numerous tests in our laboratory, we can make clear statements about the expected service life.
Do you have any questions? We are happy to support you in your design and in the selection of the suitable product