Under Heavy Load Application Conditions–Study on Maximum Service Lives of Shaft and Sliding Bearing
Yvan Cao | September 30, 2020
In a motion structure, a shaft and a bearing constitute an operating unit. In this sense, wear and friction values need to be evaluated from an overall perspective. To optimize lives, materials of the shaft and the bearing need to be perfectly coordinated, which is a main challenge for bearing manufacturers today.
For the shaft, many factors affect wear performance–A soft shaft is easy to wear, and may even cause material cracks under higher loads; and if the shaft surface is very rough, the wear rate may be accelerated. However, if a metallic surface is too smooth, a creeping phenomenon may occur, which is generally manifested as obvious noise, and may also increase wear of the bearing. To avoid the foregoing situation and to meet purposes such as rust prevention, there are actually various shaft surface treatment methods, each of which has advantages and disadvantages. This article will introduce the advantages and disadvantages through comparison, and combine iglidur® series products to obtain a work combination most suitable for your application.
Galvanizing treatment:
Galvanizing treatment on the shaft surface can generally be divided into hot-dip galvanizing and electro-galvanizing.
The hot-dip galvanizing is more suitable for guardrails and steel-structure large-scale main parts in the building field. The thickness of the galvanized layer is very large. The metallic surface treated in this way is usually rough, which will increase friction and wear. If the shaft is used in match with the bearing, comparatively, the following galvanizing method is more common.
In electro-galvanizing treatment, a workpiece is not immersed in molten zinc, but immersed in a zinc electrolyte. The workpiece to be galvanized is used as a cathode, and a pure zinc electrode is used as an anode, to form a uniform and dense electro-galvanized layer through action of current. The thickness of the galvanized layer is in direct proportion to intensity and duration of the current. Compared with the hot-dip galvanizing, this process generates a high-purity, uniform, and corrosion-resistant galvanized layer (in the electro-galvanizing process, passivation of the galvanized layer may generate an actual corrosion protection function).
As far as requirements on a pin shaft and a bearing seat and impacts on shaft wear are concerned, adverse impacts of the electro-galvanizing are dominant. An actual galvanized layer of the electro-galvanized shaft is relatively soft. In addition, passivation of the galvanized layer (“white rust”) may generate a relatively rough surface.
During a working process, a contact area of the bearing may quickly lose the corrosion protection function. In addition, whether a metallic or plastic sliding bearing is used, the coefficient of friction will increase. The corrosion protection function can be continuously maintained only if lubricating grease is added for isolation protection.
Nitriding treatment:
Nitriding treatment can generally be divided into two methods–gas nitriding and nitrocarburizing. The two methods have some characteristics in common. The longer the nitriding time, the greater the NHD (NHD–effective nitriding hardening depth). The higher the selected temperature (usually the temperature range is from 350 to 630°C), the deeper nitrogen can penetrate. However, in general, the inherent hardness of a nitride layer decreases as the treatment temperature increases. The treatment process can be simply described as follows: Alloy steel is exposed to a nitrogen-containing environment at a specific temperature, and nitrogen atoms diffuse to the metallic surface, and are combined with existing alloy elements (such as chromium, molybdenum, vanadium, and aluminum) to form hard and wear-resistant nitrides. However, increase of the alloy content may decrease the potential nitrogen penetration depth.
The main objective of the nitriding treatment is to improve the strength, wear resistance, temperature resistance, and fatigue strength of components. The gas nitriding allows partial treatment of materials. However, in nitrocarburizing, the nitrocarburizing treatment can usually be performed at 560–580°C in a salt bath (salt bath for nitrocarburizing) or ammonia (gas phase carbonitriding). The nitriding hardening depth is about 0.1 to 0.25 mm (depending on the material used). This treatment will also prolong the wear life of the shaft surface and improve the corrosion protection of the shaft surface. Therefore, the current trend is mainly nitrocarburizing.
Nitriding is suitable for almost all steel. In addition, material properties of the deep layer remain unchanged because there is no structural change. The fatigue strength is increased, and the wear resistance and corrosion resistance are improved. In addition, post-oxidation after nitrocarburizing can help to further improve the corrosion resistance. In combination with a maintenance-free iglidur® sliding bearing, due to its own lubricating property, it can run in a dry condition, that is, no grease needs to be used for external lubrication. Therefore, it is highly recommended to use two nitriding methods to reduce wear and corrosion of the shaft.
Nitriding and Electro-galvanizing
Generally, compared with untreated raw materials, nitrided materials can be used for making better shafts that are in match with the iglidur® material. Because the nitriding treatment has a diffusion depth. Even if the surface is slightly damaged, the corrosion protection capability cannot be reduced.
As described in the following example, shafts with the same material and different surface treatments are in match with iglidur®G. One of the following shafts is galvanized, and the other shaft is nitrocarburized. The result is obvious: In the area in contact with the bearing, the protective galvanized layer is completely worn. Therefore, corrosion protection is lost. The pin is severely corroded. As a result, the coefficient of friction is greatly increased.
Damage of the bearing cannot be attributed to wear in a sense of tribology. It is because the bearing material is torn due to shear stress. A set of test results of nitrocarburizing indicates that there is no negative impact from the shaft.
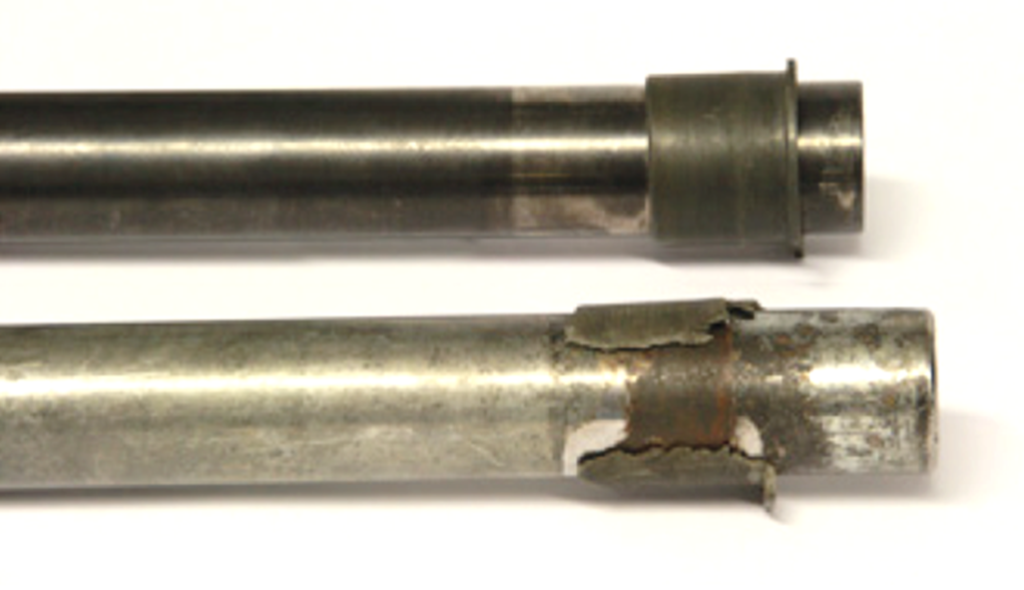
pic.1 Comparison of galvanized shaft and nitrocarburized shaft
Chromium-plated shaft
The term “hard chromium” does not refer to the actual hardness of chromium, but to the thickness of a chromium-plated layer. Generally, the hard chromium-plated layer indicates the thickness of the chromium-plated layer of at least 1 μm.
A typical hard chromium layer includes a dense network of fine cracks, which is invisible to naked eyes and inaccessible. For some applications, for example, when an oil film needs to adhere better, or a shaft is used as a piston rod in a hydraulic cylinder, the crack structure is advantageous. Even when a plastic sliding bearing is used, cracking sometimes provides advantages, because a negative impact that pairing object surfaces are too smooth can be reduced or avoided.
For the hard chromium-plated layer, all steel, nickel, and nickel alloy as well as cast iron, brass, copper, or aluminum are suitable as base materials. The hard chromium-plated surface can be in well match with almost all iglidur® materials. In addition, chromium plating achieves very good corrosion protection performance. Almost all iglidur® sliding bearings have excellent friction and wear performance in match with hard chromium shafts. This conclusion comes from practical experience of outdoor users in applications such as construction machinery and agricultural machinery, and also conforms to laboratory test conclusions under experimental conditions.
Case study: Heavy load wear test of iglidur® material
In an igus® technology laboratory, heavy load wear tests on different bearing materials are carried out by using an St52 gas nitriding shaft. Test objects: Three iglidur® materials Q, G, and Z, as well as a brass alloy bearing with initial lubrication and a composite bearing with a PTFE sliding layer. The diameters and lengths of the tested bearings are 20 mm. The test condition load is 1200 kg. Up to 200,000 test cycles are performed at a speed of 0.01 m/s (pivot angle of 60°, 30 cycles per minute) and a force of 30 MPa. However, due to severe wear, tests on the latter two bearing test objects are stopped after approximately 35,000 cycles. Only the iglidur® bearings can complete the planned 200,000 cycles.
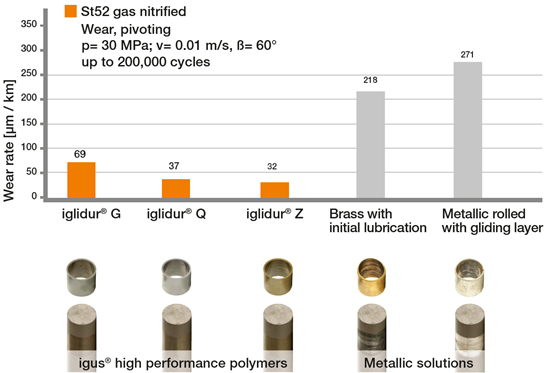
Pic 2. The shaft after the St52 gas nitriding treatment in the heavy load wear test, compared with the results of different bearing materials
The results clearly indicate the advantages of iglidur® materials. Compared with the metallic sliding bearings, wear of these three bearings is much less. Wear of the metallic bearings causes too large gap, and therefore the metallic bearings are not suitable for further use. When the wear rate is converted into the service life, the service life of the engineering plastic bearing is prolonged by approximately nine times.
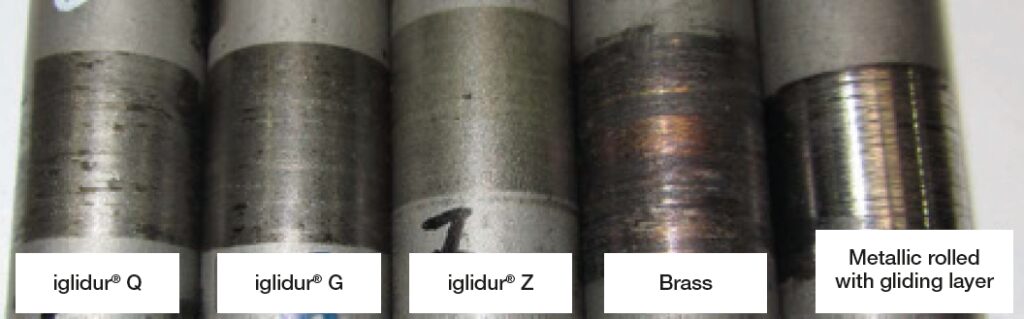
Pic 3. Comparison of shaft wear
The solution of the iglidur® engineering plastic material is different from that of the composite bearing with a metallic backing. Components of the composite bearing are applied in layers to form a combined bushing with internal lubrication and external force. The iglidur® compound is uniformly mixed in injection molding production of sliding bearings. Therefore, the iglidur® sliding bearings used in the heavy load applications (construction machinery; agricultural machinery) have the extremely low coefficient of friction while still allowing the relatively high surface and edge compression amounts. In addition, the iglidur® sliding bearings are resistant to impact and vibration.
The polymer has corrosion resistance and medium resistance. Dust, rain, mud, and fertilizer do not affect its functional reliability. Therefore, the machine can be used reliably even if stopped for a long time.
To continue to provide bearings having the best quality and cost effectiveness, intensive research and development efforts are required. Because the development in the shaft material and surface treatment field has not stagnated, IGUS Gmbh® will continue to explore and seek the perfect match between the shaft and the bearing. The future trend will continue to grow. In more and more applications, metallic bushings and rolling bearings will be replaced by bearings made of high-performance plastics.