Production of a lead screw
Kevin Huang | March 26, 2021
Rolled vs. Whirled! The manufacture of a lead screw explained briefly and concisely
How does the production of lead screws actually work? What are the processes available and what is the difference between the thread rolling and thread whirling manufacturing processes?
To find out, we should first compare the two manufacturing methods of thread rolling and thread whirling.
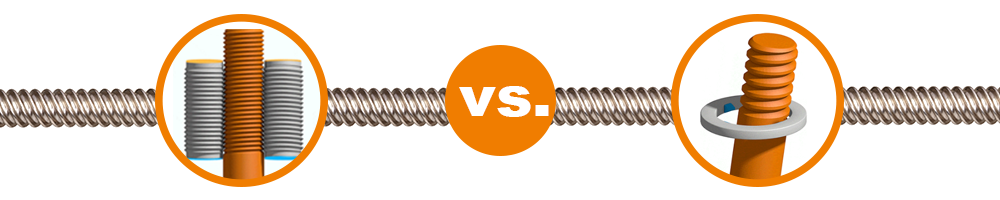
The manufacturing process of thread rolling
According to DIN 8580, the manufacturing process of thread rolling is part of the manufacturing process of shaping. In contrast to thread whirling, it works absolutely without cutting.
The actual manufacture of the lead screw is explained very easily. A workpiece is placed centrally between two tools with profile. They rotate simultaneously and the thread is rolled into the surface of the raw material by cold forming. The thread profile has been transferred to the workpiece by the compressive stress and rotation. The thread is created.
Let us look at an example of this:
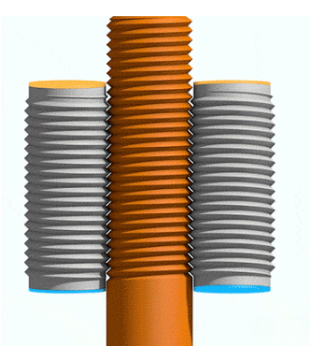
The advantages: for high volumes, this production process is faster and more cost-effective than thread whirling. One reason for this is that the material requirement is lower. In addition, cold forming achieves a hardening of the surface and higher strength. The pitch angle, the high surface quality of the rolled thread and the low coefficient of friction of the plastics result in high efficiency and a long service life of the lead screw drive.
Thread whirling production
Let us now look at the second manufacturing option. As already briefly mentioned above, thread whirling is a machining production process. Today, we dedicate ourselves to the production of the male thread.
The actual manufacturing process is also quickly explained here. Unlike thread rolling, thread whirling requires only one tool. This is ring-shaped and is clamped around the appropriate workpiece. This rotates very slowly, while the whirling tool rotates outside at very high speed. The thread is produced by inward facing cutting bits.
For a better illustration we have an example of this as well:
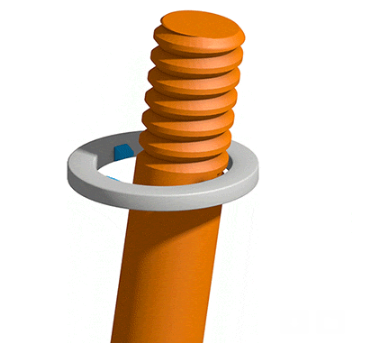
The advantages: the process is ideal for producing very precise threads that require a particularly high surface quality. This means that the surface is rougher and the edges sharper compared to thread rolling. Its flexibility makes it suitable for a wide range of thread geometries. The process is often used for materials that are not or only poorly suitable for thread rolling.
Conclusion: lead screw production
Both processes have their special specifications igus uses thread rolling as a standard process because of the cost savings, better surface finish and longer service life. Thread whirling is more suitable for small quantities and for very precise threads with narrow tolerances. It always depends individually on the required specifications and application used.