Pipetting technology for laboratory equipment (white paper)
Scott Xiong | February 24, 2021
What solution is technically best at the PoC or in an automated laboratory?
Unfortunately, there is no single answer to this question, so we will tackle it by contrasting various concepts that take into account a wide variety of applications involving automated pipetting devices.

Let’s take, for instance, a rural community practice in which the patient usually takes his (reduced) results with him thanks to small point-of-care (PoC) devices, contrasted with the big supra-regional laboratory that handles several thousand samples each day and transmits the results digitally. The latter is more extensive, but there are delays associated with transport and study depth.
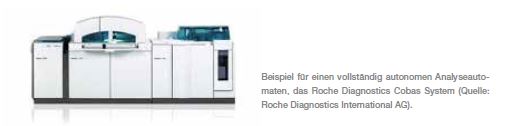
The functional scope of the equipment types used in each case, are very different in some respects, such as envisioned throughput-time ratio, functional scope of analysis and equipment weight.
This frequently puts the focus on various linear guide designs that can be used to move samples or add and remove liquids.

Read our white paper to find out how and why you should consider various systems at some points. One reason is that plain bearings cannot ensure the precision needed for the use of a 384 multi-titre plate (MTP), also known as a micro-well plate, throughout their service life. Another is that sometimes a device needs to be lightweight so that it can be used in many places. Another is that some systems can proactively rule out lubrication contamination.
Note:Whitepaper
The problem
Medicine and natural sciences are dependent on the dosing of very low liquid volumes within seconds. Thereby modern analytics increasingly requires the aspiration and dispensation by automated pipetting systems, which alone are able to meet the requirements for quantities, speed and accuracy and improve workflow efficiency. Manual pipetting as a working technique in the everyday laboratory operations of synchronous test runs and time efficiency has therefore been largely replaced through automation.
With the large number of dosings carried out in the shortest time and in parallel, the demands on the design and materials of the systems also increase. The manufacturers are therefore constantly looking for new materials and solutions to produce the ideal dosing regime for the customer requirements that are becoming increasingly complex under the specific demands of medical technology, precision and hygiene on the one hand, and under the general economic aspects, productivity and cost pressure on the other hand. Plain bearing systems made of lubricant and maintenance free tribo-polymers are an essential factor. High performance plastic plain bearings offer crucial advantages when it comes to reducing weight, cost and the required installation space.
Pipetting systems and system components
The diversity of applications has naturally led to the development of a wide range of devices. The market offers a large spectrum that covers simple “mini samplers” as well as fully integrated automated analysis systems, in which even the used pipetting needles are replaced automatically.
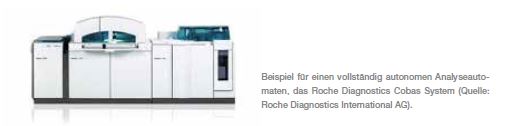
Although manual systems are still produced, the trend is clearly towards electronic and fully automated systems. The currently used devices mostly use a technology that is based on ball bearings and drives for their dynamic functions. However, innovative plastic materials and methods used in the maintenance free plain bearings technology open up a field of new possibilities in order to develop more efficient and cost effective equipment.
Basically, the devices differ according to the direction of movement in the aspiration and the number of sample vessels or pipetting heads and the channels. Thus aspirating and dispensing can be carried out by horizontal travel and vertical lift of pipetting arms or by rotation of the sample vessels. Thereby systems with individual vessels, the so-called multi-titration plates (MTPs) or rack solutions are used. For the latter two versions multiple instruments are recommended, where either multiple pipettes are immersed at the same time with one operating stroke or so-called multi-channel units with several channels and independently controllable and positionable pipettes respectively. Some systems have in addition to the two basic functions, introducing or removing sample material, still more specifications, for instance the functions to clean needles or to temper according to the chemical properties of the reagent. This must be performed by an additional pivoting function of the pipette arm. If the pipetting devices become faster, more complex and more multi-functional, the greater, of course, are the stress on the components and the length of the movements to be made. This can result in more wear and tear for the used bearings and increase the space requirement for installing the entire system. In addition, each pipetting system has its own specific demands on bearings and linear guide.

One-arm systems
One-arm systems represent the simplest form of single-channel units. Especially in the case of single vessels, one-arm systems with rotating sample holders and single round shaft solutions are used, which are moved vertically in two guide bearings. If an additional pivotal needs to be implemented, either the shaft is additionally pivoted in the bearing (so-called superimposed motion) or a non-rotating lift shaft is used, e.g. in square format, whose bearing points are pivoted on an additional mounting. For this type of movement, the plain bearing is excellently suitable because it allows superimposed motion without additional tweaks. Solutions with unrolling bodies on the other hand wear out heavily or can only be implemented with extremely complex and expensive solutions.
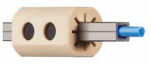
The square guide drylin® Q with a solid plastic bearing made of iglidur® J for a non-rotating and lubricant-free linear guide system (Source: igus® GmbH).
Multiple systems
Like the one-arm systems, the systems with multiple arms also possess a common suspension and operate synchronously. Multiple systems are often equipped with alternating uptakes in order to reach the different sample compartments. The suspension and control are located on a base plate, on which the pipetting heads are adapted. For vertical guiding, round shafts in a parallel arrangement or profile rail systems, either individually or also arranged in parallel, are optionally used. The installation sizes vary greatly according to the weights to be absorbed, which can range from a few grams to more than 10 kg. All solutions are acted upon by a moment of tilt from the upstream centre of gravity, which can lead to increased wear and is to be accounted for in the dimensioning and geometric design. In profile rail systems with single rail, if necessary additional torques with lateral displacement of the centre of gravity and of the drive are added. The drive elements are usually centred between the guides or are assigned to a guide side, the so-called fixed bearing. It should be noted that an adequate possibility for correcting misalignments must be ensured in the parallel construction. This can be done either with very precise alignment during assembly, if necessary with additional contact points at the base, or you can use special fixed/floating bearing combinations. Due to their 7 to 10 times higher friction coefficient, plain bearings react considerably more sensitively to eccentric loads through centre of gravity and drive than roll-off linear technology. With increasing distance of the centre of mass or drive from the bearing, the bearing load increases and thus also the driving force, thus also increasing the wear. This has to be considered in a plain bearing-compliant design and can be avoided, for example, by a previous calculation with the drylin “expert system”, which is the online dimensioning software of the igus® GmbH. Unacceptably large distance from the centre of mass and drive point can lead to the jamming of the guide elements (so-called drawer effect).
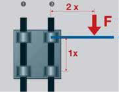
Drawer effect in case of unacceptably large distance and a coefficient of friction of μ = 0.25 (Source: igus® GmbH).
Multi-channel systems
Multi-channel systems are usually firmly connected to the traversing units and the pipetting heads. There are several individually controllable pipetting needles side by side. These can be positioned, if necessary, still with gaps to each other manually or automatically to allow the use of different sample registers. Since only one unit with a low weight needs to be moved at a time, the guide units are considerably smaller. An exception (even in the single-channel units) are systems with additional functions, such as the cap-piercing, where the closures are automatically transfixed. Since the penetration force can, like the pull-off force when removing the needles out of the closing elastomer, often amount briefly up to 50N, it is partly operated functionally identical with reinforced units and a “grabbing function” for the sample compartment or a separate hold-down function. Both require additional installation space. In practice there are three approaches that can be pursued. In the solution with miniature profile rails, the pipetting unit is usually hung with the carriage on the pipetting head and the vertically moving rail is connected to the needle carrier and accessories (such as tempering) and the drive (usually screw drive or gear rack, rarely toothed belt). The precise guidance by one or two guide carriages has a very positive effect in longer strokes. Disadvantages are a higher weight of the moving masses when using steel components, as well as the larger installation space required for the roll-off solutions and the external drive. Another disadvantage is the much higher cost of this solution with corrosive media in the operating environment. A good alternative is provided by round shafts systems with plain bearing. In these widely used systems usually the drive gear racks are already incorporated in the round shafts. Moreover, the round shafts can be constructed as a hollow body, whereby the needle carrier, tempering and drive become one unit. The plain bearing can be thin-walled and incorporated in the head. The anti-twist protection of the rotary shaft in the bearing is produced largely through the drive toothing and the drive pinion. This system is very cost effective in the standard configuration, as well as in combination with anti-corrosive round shafts. With very high demands on the permissible operating cycles, there occurs sometimes the problem of increasing wear of the bearing and with it a change in the positioning accuracy. This can be compensated by pretensioned solutions that make up for the bearing wear somewhat by readjusting springs. In terms of positioning accuracy, the structure with triangular and rectangular guide systems is also easier to control in the long term coefficient, plain bearings react considerably more sensitively to eccentric loads through centre of gravity and drive than roll off linear technology. With increasing distance of the centre of mass or drive from the bearing, the bearing load increases and thus also the driving force, thus also increasing the wear. This has to be considered in a plain bearing-compliant design and can be avoided, for example, by a previous calculation with the drylin “expert system”, which is the online dimensioning software of the igus® GmbH. Unacceptably large distance from the centre of mass and drive point can lead to the jamming of the guide elements (so-called drawer effect).
Tribological comparison of plain and ball bearings in the linear guide
A major challenge to every appliance used in the analysis is the prevention of any contamination of the sample material. Traditional guide systems usually use rolling bodies (commonly also called ball bearings) to implement lift and travel movements. Except ceramic systems, which are hampered by the disadvantages of high cost and low tensile and flexural strength, those with rolling bodies, which mostly consist of metals, however require the use of lubricants. In general, they are characterised by very low movement forces (μ > 0.02-0.05) depending on their sealing systems. Because of their different centres of mass, systems with drives that are widely separated from each other and high tilting moments can be used. Due to the roll-off movement, such systems should be constructed from materials with “hard” surfaces, as otherwise material abrasion (so-called pitting) can set in on one rolling partner and in the worst case, lead to the “jamming” of the elements. Harder surfaces indeed reduce the contact area, but can lead to increased wear due to their brittleness. A constant lubrication is therefore essential for the smooth movement of the components in contact. The lubricating film also ensures a slight corrosion protection. However every lubricant entails in principle the risk of contaminating the reagent and thereby lead to “falsified” results. Furthermore, the contamination and the use of generally oily lubricant can ultimately lead to the failure of the entire system, which can only be remedied by costly maintenance.
The use of plastic plain bearings is therefore a sensible alternative, particularly for the linear motions of analytical and pipetting systems. This is true despite the poor coefficients of friction of dry gliding systems (μ 0.08 to 0.15). In the application case of the “pipetting needle”, this is usually of minor importance, because the introduction of force should be made by the mass of the pipetting needle and additional forces centrically in the axial direction as in the cap-piercing, which is ideally surrounded by the guide element. Since the frictional movement takes place on large parts of the surface, the pressure loads and demands on the surface hardness are correspondingly low. This enables the use of “soft” and inexpensive materials. For the pipette holders (i.e. the pipette axis), for example, simple VA materials with ground surfaces can be used, which are easier to machine and cheaper to obtain. Likewise, requirements for special functions, such as hollow profiles, can be easily implemented. The installation space required is thereby considerably reduced. In addition, the differences in friction coefficients are compensated by the lighter plastic material, which enhances the dynamics of the linear guide. Considered as a whole, the conventional guiding systems of pipetting devices lose their traditional advantages, positioning accuracy and low friction coefficients due to the ball bearings, and face stiff competition from the comparative advantages of plastic solutions.
Incorporated lubrication, freedom from maintenance and flexibility of iglidur® plain bearings
The freedom from lubricants is however the main advantage of plastic plain bearings. The solution of igus® GmbH is expressed by the name “iglidur”. Since three decades this trade name has been representing a proven serial material for polymer bearings, which is based on the concept of incorporated lubrication. In addition to the basic component of base polymers, which ensure minimum wear and abrasion, iglidur plain bearings made of plastic compounds have physically bound additives of selected solid lubricants and fillers. The solid lubricants are embedded in the bubbles of the plastic material and thereby protected. They are successively released only due to the emerging micro wear . And while the solid lubricants thus ensure the constant, oil compound-free dry lubrication of the bearing, the fillers increase the resilience and influence the material properties in other positive aspects. Since no surface coating needs to be
carried out as in metal bearings, the lubrication is continuously regenerated and is protected from complete loss even under the influence of chemicals, for example through washing. The system of the incorporated lubrication makes iglidur a material permanently optimised in wear and friction, which guarantees a minimum maintenance. Moreover igus® is able to make detailed statements on the service life of the respective iglidur bearing as a result of the intensive research in its own lab, which is the industry’s largest, where 140 trillion test movements are carried out annually solely in the plain bearings division, and thus provide the user with a unique design and operational safety. By manufacturing through the injection moulding process, iglidur can be produced variably in accordance with the individual requirements of the user. Here, a variety of options opens up also in terms of the shaping of the linear guide. Gliding movements can be developed with plain bearing-guided systems in almost any scenario. Systems with a round shaft guide and a triangular guide profile, with and without clearance compensation respectively, are already in use. In addition there are alternative products with an identical outer structure, guide carriage and guide rail. With more than 7,000 products made from 30 different iglidur material groups the options for the construction are virtually unlimited.
Polymer solutions for drive technology
In addition to the application possibilities of high-performance plastics in plain bearing technology, lubricant-free and friction-optimised materials can also contribute to efficient solutions in drive technology. The variability of the gliding guide systems is carried forward in the integration of the drive systems. The drive can be integrated without additional components, so that no additional space is needed. Gear rack profiles can, for example, be installed in the used travel axes. Optionally, the design can be carried out in such a way that the media are conducted safely and compactly inside the profiles.
Two application examples of integrated solutions for gliding systems, including igus® measurement cable / energy supply system (Source: igus® GmbH).
Even though ball guided solutions for pipetting is the most common method today, the gliding guide has established itself for a long time and is already being used successfully in many cases. Contrary to the preconception that the desired precision can only be achieved by the use of conventional systems, structures specially designed for the gliding guide already offers at least equivalent results in terms of accuracy. In many other respects, however, the innovative technique is superior. Because the system of the gliding guide in combination with innovative bearings made of tribo-polymers provides altogether the following significant advantages for the producers of pipetting systems:
- Tribologically optimised plastic bearings reduce the weight of components and thus the weight of the overall system.
- The lightweight materials increase the dynamics and balance the differences in coefficients of friction.
- Due to the potential integration in structures, significantly less space is required.
- The systems can be mounted and dismounted more easily and flexibly and are resistant to media.
- The service life of components can be determined precisely in advance.
- Working area and reagent are not contaminated by lubricants.
- Ultimately plain bearing systems are less expensive than their “metal” competitors. They are at the same time more efficient in operation and in costs.
The igus® GmbH offers under the term “dry-tech bearing technology”linear guides, materials and components made of tribo-polymers, which have been tested in the in-house technical centre since decades and proven in daily practice in the laboratory. The company has thus established itself internationally as a supplier for laboratory equipment manufacturers and with its expertise in innovative plastics technology offers perspectives for a new generation of high performance and cost effective automated analysis systems.

The basis for this position is the consistent orientation of the research and development department of the igus® GmbH on the specific needs and concrete problems of medical technology. The close collaboration often results in pioneering new solutions, where hi-tech plastics prove to be an ideal material not only for the bearing technology. The most recent example of this is the “e-cord micro”, which guides even the smallest hoses in the millimetre range safely and flexibly. The miniaturisation of devices and components is a key challenge to every manufacturer of laboratory or medical devices. This reduction of the installation space, however, can only succeed if energy and media supply keep pace. The “e-cord micro” made of a tribo-polymer tape even holds capillary tubes with less than a millimetre in diameter. The modular design enables it to optimally adapt to every installation space and every direction of movement. Fixed bending radii prevent the bending of the cables. Thus the design and friction-optimised tribo-plastics ensure long term reliability and maintenance-free, high operating times.
To learn more about this, please click here: