Exoskeleton – Bionics pure
Scott Xiong | September 28, 2020
Widespread in the animal kingdom, for people an option. The skeleton on the outside of arthropods provides stability in the same way as the endoskeletons of mammals.
Why not combine the advantages of the two systems with each other?
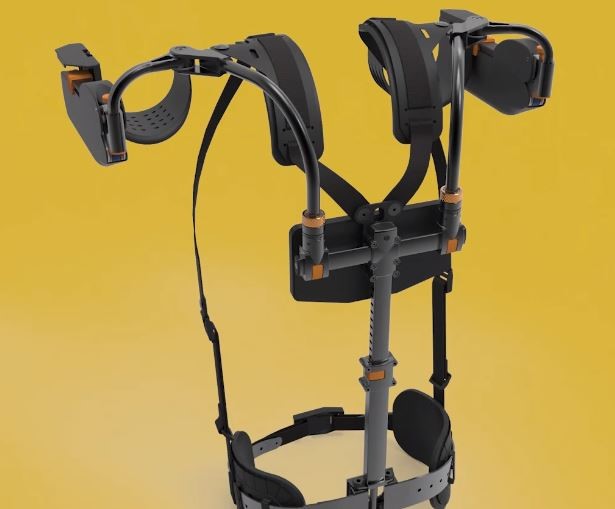
An endoskeleton (inside the body) is strong but, having numerous joints, is nevertheless very flexible. It is located at the centre of the axes of the body and extremities. It is supported by muscles and ligaments that hold the individual flexibly interconnected parts together and support them while channeling force at the same time.
This makes lifting, holding, standing up and so on possible, namely everything for which strength is needed in a lever.
Requirements for industrial use
In today’s everyday world of work, however, there is a need for more applications of force and a greater degree of monotony than many bodies would be able to cope with. Whoever paints a ceiling at home every few years or so as a do-it-yourselfer, having to hold the paint roller high and bend their head backwards at the same time, can easily imagine why certain branches of industry have increased rates of people being written off sick by a doctor, if they do certain kinds of work.
In a health insurance evaluation from 2017, unfitness for work due to problems with the musculoskeletal system came in second place in the rankings of illnesses that result in time off work.
Source: TechnikerKrankenKasse TKK Statistics of the most common reasons for a doctor’s certificate 2017
Not only an incorrect sitting posture or unergonomic workplaces are of interest, but also the work itself. The results of frequent lifting, overhead work and continually recurring movements are also reflected in the statistics.
The supporting exoskeletons are a way of dealing with these stresses.
Active or passive? Activity is always good, but:
In general, a distinction is made between two types of exoskeleton, “active” = systems driven with actuators and an external energy supply, and “passive” types, which support the body by providing the necessary force via balancing systems, thus relieving the muscles and skeleton.
“Passive” exoskeletons are fly weights with extra strength.

This leads us to make a comparison with a weight lifter (up to 1977, the class “up to 55kg” was still officially called “fly weight”), world record of the class up to 56kg today: 171kg in the clean and jerk discipline.
The world record holder in the highest weight class (> 105kg) “only” achieves: 264kg.
The lightweight can move more than 3 times its own body mass, the heavy athlete only achieves approximately 2.5 times his own body weight.
The passive exoskeleton is clearly based on inspiration from the area of bionics
While the arthropods use e.g. light limestone or chitin for their armour, industrial exoskeletons have to be worn by people. This puts limits on the weight and service life of the device. If the arms are reinforced but the support on the back is so heavy that it causes pain after a short time, a compromise has not been found.
Greater use is therefore made of the advantages of polymers. First of all, the weight. Framework components and springs, if possible made of composite materials such as CRP, use of metal materials only where really necessary, whereby titanium or aluminium are good choices if metals are unavoidable.
Due to the connections joining the individual joints to the exoskeleton (here, it is best to work directly parallel to the “real” joints), there are many different joints.
THE main advantage of polymer:
THE advantage of polymer is already evident: 80% less weight but the same installation space needed. The following is an example of identical components according to ISO 3547-1 for plain bearings. Very important for efficiency but not only in vehicle manufacturing.
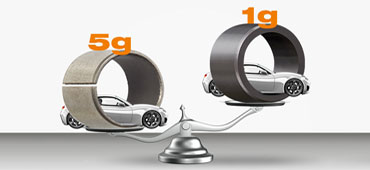
The comparison of a further type of bearing also with an inner diameter of 10mm:
multiplied by a factor of >3 the comparison of ball bearings: approx. 6 to approx. 19 grams – (*) Size 6000-2RS (polymer with labyrinth seal)
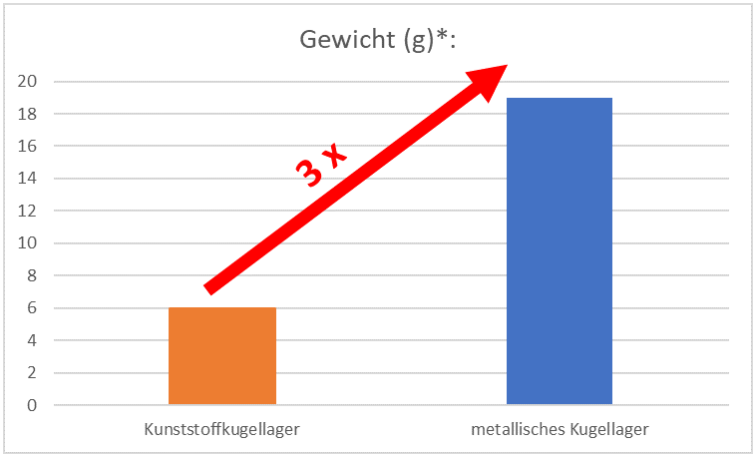
A further advantage for polymer solutions “unusual bearing pins”
To continue the theme of lightweight construction, the pins, which are moving and load bearing elements, should not be overlooked.
Aluminium e.g. is three times lighter than steel, but also more sensitive to bending. In other words, the whole weight advantage cannot be exploited; larger dimensions must be chosen if the same flexural strength is to be achieved. However, not until the weight advantage is used up…. Experience shows that a factor of 1.3 to 1.5 is sufficient.
In the case of titanium, larger dimensioning is hardly to be expected.
Friction and wear
The crucial points in plain bearing design. Firstly: ball bearings (if external factors such as dirt, corrosion and so on are ignored) will foreseeably not wear out and will have the best coefficient of friction. Nevertheless: they are usually too heavy and too expensive.
If the coefficient of friction of common plain bearings on selected pin materials are considered, clear differences can be detected. (All tests carried out in a rotation test at igus® under the same conditions)
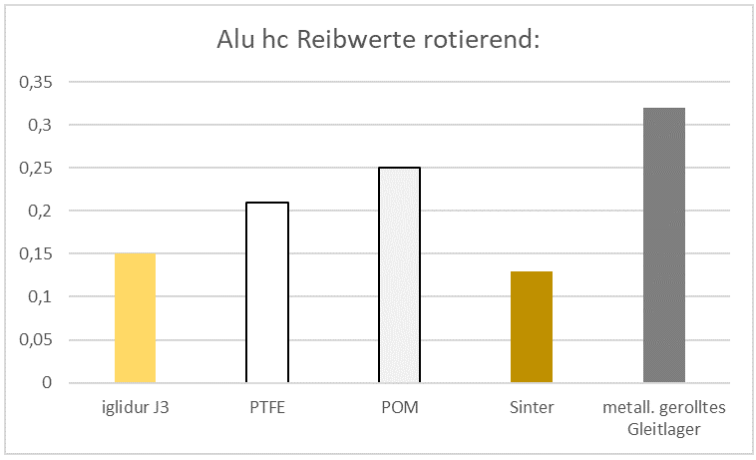
The situation is the same with the wear rates of the components on these “lightweight shafts”.
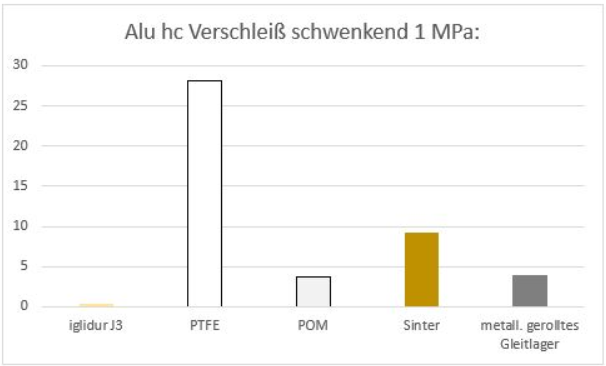
All in all, good reasons for the use of polymer plain bearings. As a pioneer of exoskeletons for use in the home also reports, for example:
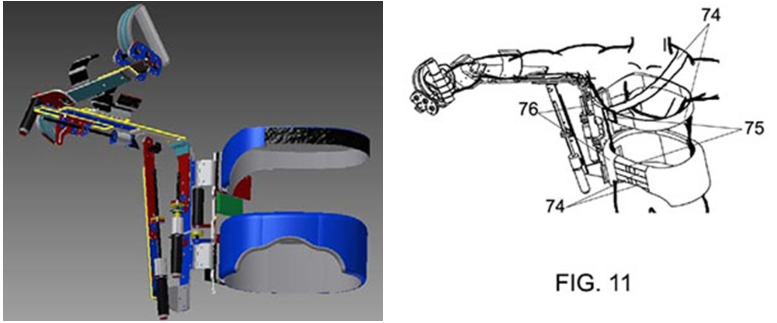