Discussion on Color Difference of drylin® Hard Anodic Oxidation rail/ Shaft
Kevin Huang | September 10, 2020
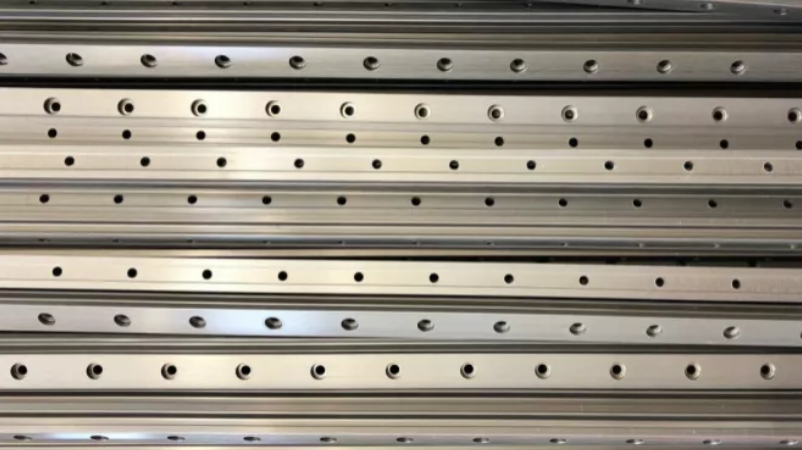
We get asked this question quite often, the brief explanation by sellers sometimes cannot be accepted by or not satisfy customers!
Of course, we do fully understand the customers’ complaints about this situation. For example, the customer is designing a device, the linear bearing system involved is of great importance for them, which may also involves that these guides will be taken as the outer parts. The customer will receive a batch of dark champagne guides later. While a month later, the customer purchases a new batch of steel guides, and finds that the color of this batch of guides is lighter than that of the last batch. In this case, the customer may have a machine or a device with two different linear rail systems in color, which may not satisfy the customer!
Here, we hope to make a technical specification for this phenomenon, so that the reason why this situation happened is understandable. Can it be avoided? Then try our best to give the customers who require the products with the very same appearance some possible solutions!
Product material – aluminium alloy
The linear bearing products like drylin guides or shafts are extruded with the 6060 – T66 raw materials, it is the material we use in general and is suitable to produce the guides or shafts of high production requirements with relatively small deformation.
The traditional sliding bearing is generally used in combination with a bearing steel shaft or a stainless steel shaft, while when the igus sliding bearing and the aluminium alloy guide or shaft are used in combination, the huge benefits will be brought.
Due to the lighter weight, lower cost, and better corrosion resistance and heat dissipation of the aluminium alloy guides or shafts, the gathering of the friction heat is reduced which prolongs the service life, and the aluminium alloy is easier to be processed than the quenched steel.
We have cooperated with many machinery factories, and they generally are reluctant to process the HRC 50 – 65 steels or the stainless steel shafts while more willing to process the aluminium alloy products.
Surface treatment – hard anodic oxidation
The hard anodic oxidation treatment of the aluminium alloy will make its surface have good abrasive resistance, high chemical resistance and high hardness. The surface is a technical surface rather than a decorative one. There may be discoloration and slight cracks which have no impact on the corrosion resistance, abrasive resistance or the performance of the bearing. Please note that once the guide or the shaft has been cut or processed, the finished surface is free of the oxide layer, and it is the aluminium alloy body.
So what is anodic oxidation?
The part anodic oxidation is the cathode (anode) of the primary battery
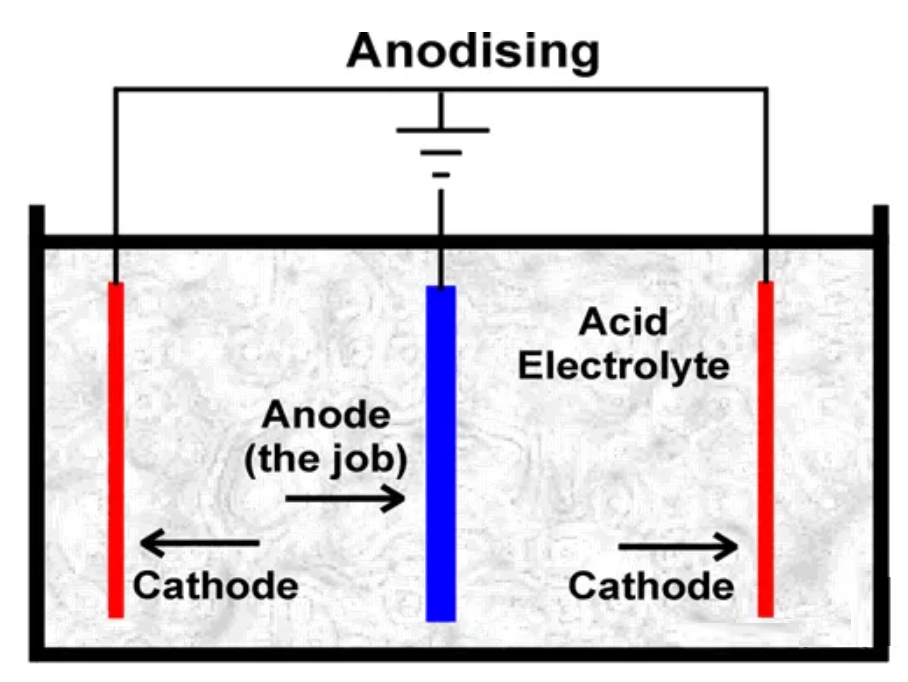
Anodic Oxidation Schematic Diagram
In fact, this is a chemical reaction that the aluminium is experiencing, it is an oxidation process. In this way, the surface is connected with the aluminium underneath, which can not be wiped off like paint.
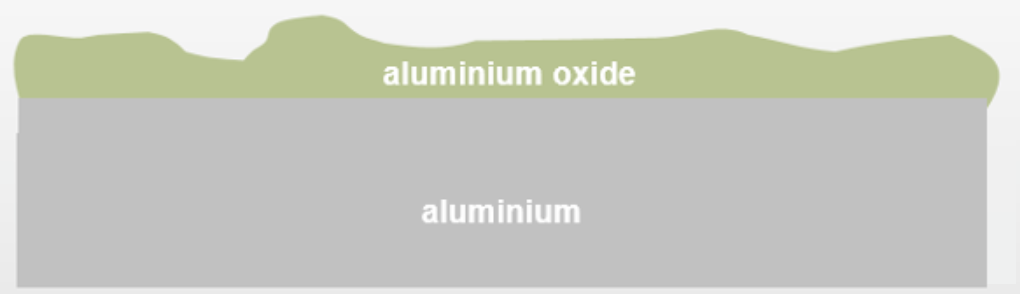
The reason why there are color differences on the guides or shafts treated with hard anodic oxidation:
We can control the tolerance of the guides or the shafts through the thickness of the oxide layer to some extent (very strictly)
For example, the IGUS® label of the WS – 10 guide in the product sample is 10.0 mm (+/- 0.1). In order to ensure that the maximum deposit volume of the anodic oxidation has no adverse impact on the bearing fit, we specially reduce the size of the guide after the aluminum alloy extrusion and try to control the time of the anodic oxidation, so as to make the outer diameter of the guide close to 10 mm as much as possible. This aims to reduce the clearance in the whole bearing system.
If the dimensional tolerance of the component extruded is close to the upper limit, we will control the minimum thickness of the anodic oxidation layer in accordance with the anodic oxidation specification as required on the drawing (It is generally the Mil-A-8625F Typ Ⅲ Class 1, or the similar EU specifications). This will produce the guides or the shafts with lighter colors, which still meet the igus quality specification of the anodic oxidation thickness.
If the dimensional tolerance of the component we get from the extruder is close to the lower limit, we will put the component into the oxidation tank for a longer time to increase the thickness of its oxidation layer, so as to ensure the dimension can reach to the nominal 10 mm as close as possible, which will make the color of the guide or the shaft darker.
In addition, the changes of some micro chemical elements, the slight differences of the oxidation pond and the oxidation solution in different batches, the PH control in the oxidation process, the control of the purified water cleaning and others all may cause some impacts that make the color control more complex.
Generally speaking, we should ensure that the minimum thickness of the hard anodic oxidation is 30 µm with the maximum thickness less than 130 µm.
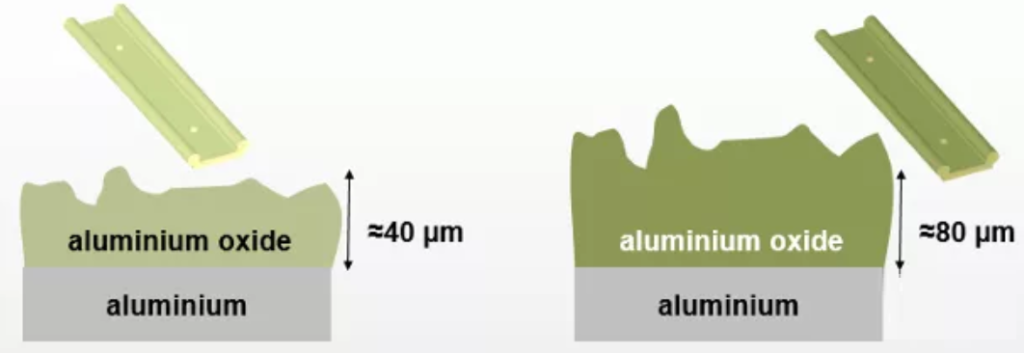
aluminium oxide
We promise that the color of the guides or shafts in the same batch is as close as possible or the same.
In case that the customer has a high requirement of colors, we suggest the customer to choose black hard anodic oxidation or colorless ordinary anodic oxidation which rarely causes color difference!
It should be noted that the thickness of the oxidation layer has no impact on the bearing service life, the reason why we use lots of hard anodic oxidation parts is that our linear guides are often used outdoors or in factories, so the good abrasive resistance is necessary and also such parts can prevent the damage caused by the environment.
One more thing should be emphasized here is:
The complete hard anodic oxidation must be treated with the last process of oxide film “sealing”!
In the process of electroplating, due to the impact of the power supply polarity, the anode is always formed as the porous structure with high surface activity, which makes the contaminant or the erosive substance easily access to the pores, meanwhile the internal dyeing of the coating or the colored chromatophore may outflow, which may lower the surface activity of the coating.
The anti-pollution capacity, corrosion resistance, abrasive resistance and light resistance of the coating can be improved through the sealing treatment, so as to ensure the performance stability of the coating. The anodic oxidation workpiece must be sealed.
Facts have proved that only sealed oxide film can have the sufficient protective effect. The sealing of the anode oxide film aims to seal the celluar clearance generated in the electrolytic process, so that the oxide film can have the proper protection value, otherwise, the oxide film can absorb the contaminant or the corrosive substance due to its good adsorption performance. Therefore, the corrosion resistance of an oxide film without the sealing treatment or with poor sealing treatment is worse than that of a natural oxide film under some circumstances.
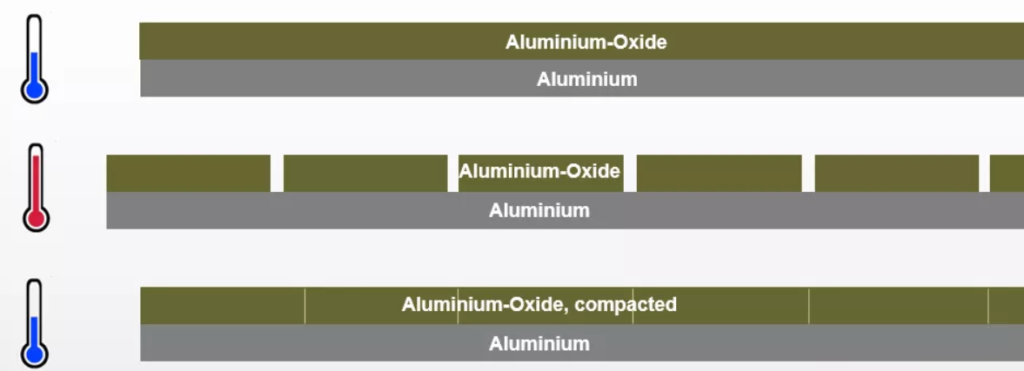
Sealing treatment of the oxide film
Purposes of sealing treatment:
- Prevent the poor appearance of anode oxide films.
- Improve the weather resistance of anode oxide films.
- Improve the pitting corrosion resistance of anode oxide films to the greatest extent.
- Minimize the fading of the colored oxide films.
- Improve the anti-erosion ability of anode oxide films.
- Improve the electrical insulation performance of anode oxide films, especially the insulating properties in wet environment.
Sealing is often the last step in anodic oxidation treatment
While after this process, there will be some slight cracks visible to the naked eye on the oxidized surface, this is the sign of the hard oxidation! Therefore, some customers raise a so-called appearance quality problem, we can make appropriate explanations!
Technically speaking, the color of a guide or a shaft is not so important that can affect the performance of the products.
Welcome to contact us if you have any questions or needs!
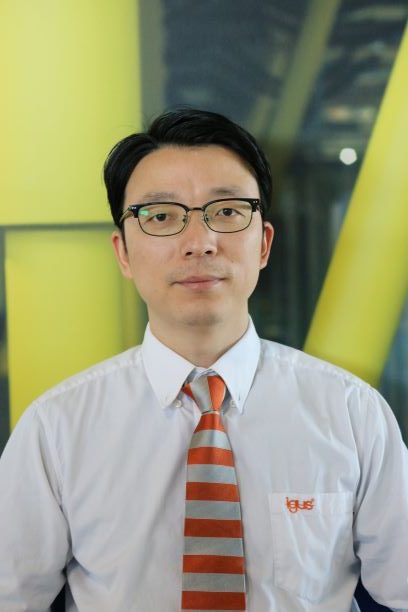
黄先生 (Kevin Huang)
Tel. 021-8036 6699
M.P. 13816366092
khuang@igus.net