How do iglidur plain bearings reduce noise in automobiles (Buzz, Squeak and Rattle)?
Martin Liu | March 29, 2020
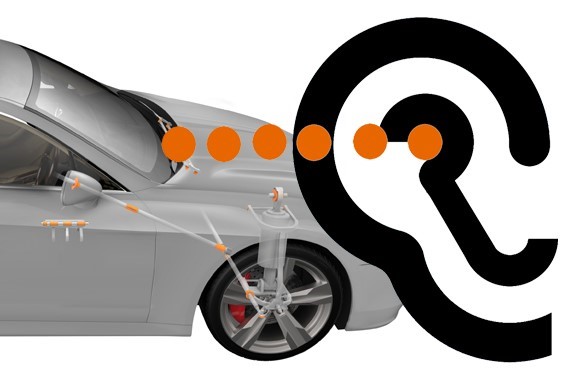
What is Buzz, Squeak and Rattle (BSR)?
BSR are all noises that are produced by components and
assemblies in the motor vehicle. BSR testing, also called a noise and rattle
test, is an acoustic method from the automotive industry and is used to measure
the volume of these noises. A realistic situation with corresponding vibrations
is simulated and the volume of the noise is then measured. The technical
challenge for the vehicle and component engineers is to identify the ‘noisy’
components and replace them with a quieter solution wherever possible.
The expectations of the OEMs in this context are increasing continually. In the
case of alternative drives such as the hybrid or electric motor, the noise of
the drive is reduced, as a result of which noises inside the vehicle are masked
to a much lesser extent by a loud combustion engine. At the same time, it is
becoming quieter and quieter inside motor vehicles.
How do iglidur plain bearings reduce noise?
Noises
always arise where components interact with each other, in other words where
friction occurs. With the tribologically optimised high-performance polymers
from igus, you achieve an especially low coefficient of friction and therefore
a quiet application. Whether in vehicle seats, hinges or actuators, the variety
of applications for our iglidur plain bearings inside vehicles is great.
Polymer is characterised by the fact that, unlike metal, it has a damping
effect. In applications involving severe vibrational stress, a polymer bearing
solution helps to reduce noise inside motor vehicles. The range of materials
developed by igus includes materials that have especially good damping
properties.
More reasons for using iglidur in automobiles can be found here: https://www.igus.eu/info/5-reasons-for-the-use-of-iglidur-plain-bearings-in-automobiles